今天在此为大家研究了82,68两种金刚石取芯钻头的激光焊接方法及工艺,并分析了激光焊工艺参数对焊接质量的影响。此技术已成功地应用于实际生产中,并对同类产品有指导意义。金刚石取芯钻头不仅在地质勘探中有重要地位,更因为其具有钻进速度快、石材损耗小、不破坏周边环境等独特优点而被广泛应用于大理石、花岗石、钢筋水泥墙面的钻孔。下面就让我们一起来了解下金刚石取芯钻头的激光焊接方法及工艺吧!
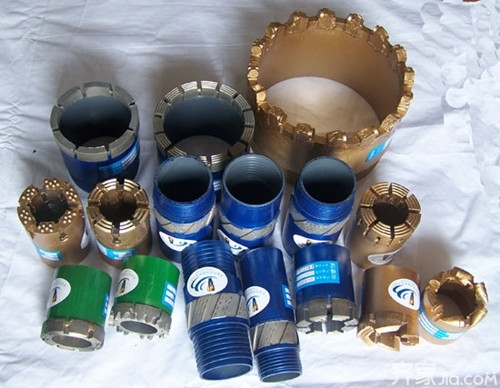
金刚石取芯钻头不仅地质勘探有重要地位,更因为其具有钻进速度快、石材损耗小、不破坏周边环境等独特优点而被广泛应用于大理石、花岗石、钢筋水泥墙面钻孔。金刚石钻头钢基体上连接一种由金刚石胎体材料热压而成一种复合烧结体,常称之为刀头。国内钻头常采用钎焊方法连接。金刚石取芯钻头工作时由于转速极快,受强烈冲击震动,需要高剪切强度高温强度。钎焊钻头刀头经常由于高速钻进发热引起钎料熔化而脱落。所以,国外从80年代后期就发展用激光焊代替钎焊,激光焊与钎焊比较有如下优点:由于基体与刀头冶金结合,强度高,刀头不易脱落,特别无水情况下;焊缝为细小均匀柱状晶组织,不易产生裂纹,保证钻头高速钻进时不致于开裂而产生危险;焊缝热影响区极窄,对金刚石没有影响,保证了产品最佳性能;易于实现自动化,效率高,质量稳定可靠,并且产品平均成本低。
金刚石取芯钻头结构。目前国外市场需要激光焊钻头几乎与激光焊锯片相当,市场潜力很大,利润也相对较高。由于金刚石取芯钻头刀头粉末冶金材料,不可避免地存孔隙,焊接难度大;基体与刀头异种材料焊接,刀头比基体厚,难于双面焊接,所以比起金刚石圆锯片来焊接难度更大,目前国内还未发现这方面报道。我们经过几百次试验探索,取得了较好效果,成功地解决了关键技术,现已应用于实际生产,产品全部出口,用户反映良好。
1.试验装置及方法
试验在美国进口快速纵流激光器上进行,该机美国80年代先进产品,型号为EFA-51,输出模式为TEM00TEM01,最大输出功率为1500W。选用f=100mmGaAs聚焦透镜,通同轴保护气体Ar气以保护焊缝及透镜。钻头基体刀头被装夹专用夹具上。回转工作台能带动夹具及钻头作圆周运动,并且能一定范围内调节角度。激光束稍偏于基体一侧,并采用一定负离焦。为使刀头基体吻合良好,刀头焊前须磨弧、去毛刺,以免漏光损失能量;为减少焊接缺陷,焊前必须去除焊接部位及其附近油污、氧化皮水分。
基体材料为普通45#钢,经调质处理,厚2mm;由于金刚石高温下易石墨化,激光焊接时会焊缝出现空洞,所以,刀头需设计1.5mm~2mm过渡层,我们通过大量试验,选取一种特殊Co混合物作为过渡层,刀头厚3mm。
钻头焊后,目测用10倍放大镜观测焊缝外观,检验焊缝有无气孔、咬边、裂纹等宏观缺陷,然后采用DSA标准用专用弯曲强度检测仪检验每个刀头弯曲强度。
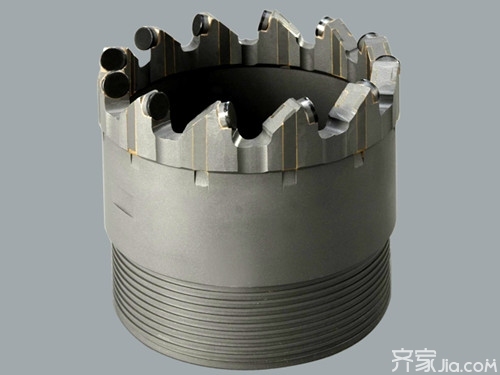
2.试验结果及分析
2.1 材质分析
基体材料激光焊条件下有较好焊接性。刀头则不一样,由于粉末冶金材料,焊接时极易出现气孔甚至空洞,当焊接参数不当时,还会产生裂纹,极大地影响了焊接强度。刀头性能对焊接性能影响非常大,机械性能好且致密刀头激光焊条件下,只要焊接参数选择得当,就能得到符合使用性能焊缝,其抗弯强度可达到或超过1800N/mm2,断刀头。材料一定时要使刀头性能优良,首先必须提高刀头压制密度,可采用选择颗粒细、形状均匀之粉末压制,另外,不影响金刚石性能前提下,尽量提高烧结温度压制压力,并选择合适保温时间对提高刀头机械性能很有必要。刀头内不可避免存孔隙,刀头密度不能达到理论值,但合适压力、温度以及保温时间、粉末混合时间及速度都刀头致密均匀重要保证,从而保证有良好焊接性能。试验表明:当单位压力20MPa左右、温度800℃左右、保温时间为4min时,即可得到能满足激光焊需要、又不损坏模具及金刚石性能刀头。刀头密度对焊缝强度影响最大,低密度刀头焊接出来焊缝强度很低,几乎不可能达到所需强度。
2.2 焊接工艺研究
焦点位置光路系统一定条件下,焦点相对于材料表面位置对熔深、熔宽、熔化效率影响很大。本试验,采用负离焦可以增加熔深,离焦量约为0.3mm,为减少焊接时飞溅,保护透镜,降低刀头材料合金元素烧损,焦点应偏向基体一边0.1mm左右;为获得最佳角焊缝效果,入射激光应倾斜6°~11°左右;反面焊接时,我们光路系统增加一个反射镜,置于钻头基体筒内,将激光束反射到所须位置,,成功地解决了钻头因单面焊接易出现强度不稳定问题。
激光功率密度
激光功率密度决定焊缝穿透深度主要参数。光斑直径一定情况下,功率密度正比于激光功率。功率越高,允许焊接板厚越大,焊接速度越快,生产效率越高,但过大激光功率会使焊缝外观变坏,由于溶池翻滚,易产生一波一波突起空洞,严重降低了焊缝有效承载面积,抗弯强度降低;即使焊后检验能达到所需强度,切削过程因为应力其,裂纹由孔洞处扩展,出现明显疲劳断裂特性;此外,高焊接功率还会使熔池化学物理反应剧烈,飞溅增多,污染透镜;由于过渡层材料与金刚石胎体材料热胀系数不一样,过高焊接功率条件下,易两层相接处由于过热而产生裂纹。双面焊接?82钻头,光斑直径为0.4mm时,用功率900W能取得较好焊接效果。试验我们发现,采用小规范焊接方法焊接钻头能取得好焊接效果。比起金刚石圆锯片而言,焊接钻头激光功率要相对高些,这因为激光入射圆钻头基体上被部分反射掉缘故。
焊接速度
焊接速度同激光焊接功率一起影响着焊接区域热输入,因而对焊缝形状尺寸有较大影响,随着焊接速度增加,焊缝宽度降低,熔深减少,生产率提高。过大焊接速度会使焊缝无法穿透,强度降低,而且焊缝有害气体如N2,H2,O2及CO来不及逸出,使焊缝气孔增多,影响抗弯强度焊缝外观;当焊接速度太低时,焊缝太宽,热影响区过热,晶粒粗大,有时还会产生裂纹,特别两层相接部位产生裂纹,严重地影响了焊接质量,并且刀头合金元素烧损严重,影响了刀头综合性能,焊缝部位因为熔池翻滚而出现一个一个空洞。我们试验,对于?82,?68两种钻头各50个,激光功率选定为900W,转速分别为8r/min,9r/min时,其焊缝弯曲强度都达到超过4000N/mm2,随后切削过程,也未发现掉刀头现象。
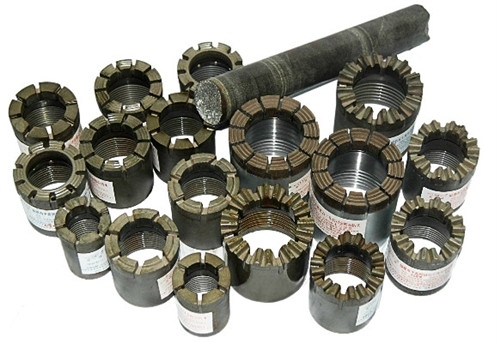
保护气体流量
保护气体激光焊接过程作用有三:保护焊接区不被氧化;保护聚焦透镜;吹散部分等离子云。若气流量太小,起不到作用,焊缝区被氧化而引起机械性能恶化,透镜也易污染损坏,成本增加;过大气流量会吹翻熔池,影响焊缝成形,增加焊接缺陷,同时减少熔深。我们焊接试验选用气流量为0.5L/min。
结语
(1) 要使激光焊接金刚石取芯钻头成功,刀头配方一定情况下,必须使刀头致密而且机械性能良好;
(2) 激光焊接金刚石取芯钻头过程,必须合理地选择有关工艺参数,如激光功率密度、焊接速度、焦点位置及保护气体流量,才能保证焊接质量;
(3) 采用小规范焊接工艺焊好钻头有效途径;
(4) 采用光路系统增加一个反射镜方法可以进行钻头反面焊接,解决了钻头因单面焊接结合强度不稳定问题,但这种方法不能焊接直径太小钻头;
(5) 激光焊接金刚石取芯钻头方法还不适应大批量生产,生产率不高,有待进一步改进。
编辑总结:以上就是金刚石取芯钻头的激光焊接方法及工艺的相关介绍,希望能够帮助到有这方面需求的朋友们!如需了解更多相关资讯,请继续关注我们网站,后续将呈现更多精彩内容。您也可以上齐家商城购买更多你心仪的产品哦!